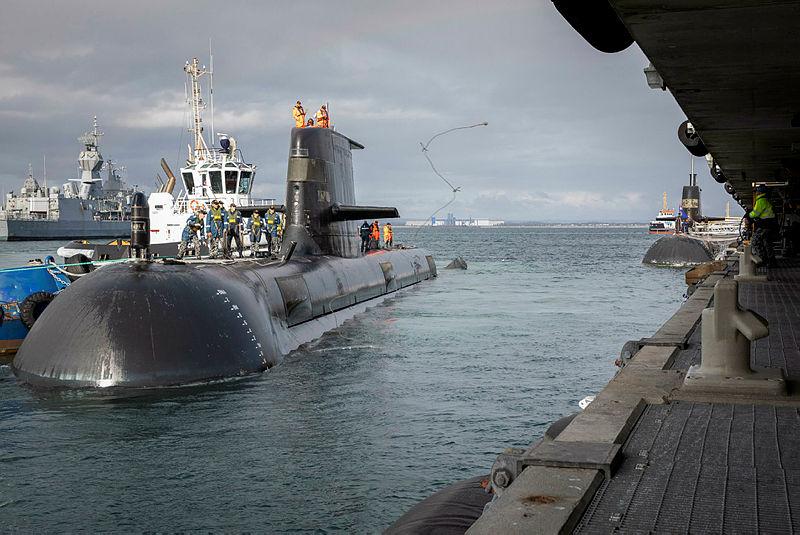
In view of Derek Woolner’s warning last month that the Royal Australian Navy’s new Attack-class submarines will be obsolescent by the time they’re delivered, it’s time to revisit the main storage battery question—including what we’re trying to achieve, the implications for submarine design and build programs, the state of the art, and what is actually being delivered.
For any submarine, safety is paramount. We want our submariners to come home safely from their patrols. Life is dangerous enough under the sea without adding to the risk.
A fire in a dived submarine can turn it very quickly into a tomb. Any proposed new type of battery must be able to pass a rigorous safety case to ensure that the risks are thoroughly and reliably mitigated. That will be difficult for a chemistry like lithium-ion, which contains its own oxidant and has a development history of unquenchable fires (for example, the US Navy Advanced SEAL Delivery System, the Boeing 787 Dreamliner, mobile phones and laptops and, more recently, the Russian Losharik disaster).
Derek Woolner and David Glynne Jones build a case for light-metal batteries in their three-part Strategist series titled ‘Future-proofing the Attack class’ (‘Part 1: propulsion and endurance’, ‘Part 2: performance and capacity’ and ‘Part 3: regional superiority’).
There are fundamental flaws in their argument. In part 3, for example, they assume that the technology for utility storage systems is directly transferable to submarine propulsion systems. They’ve also failed to understand the nature of submarine design and the impact of the battery.
The size, type and design of a submarine battery must be matched to mission requirements. Utility storage facilities are generally spread out over a large area and are isolated from neighbours. The South Australian Hornsdale Power Reserve—the Tesla battery—covers almost 10,000 square metres, nearly the size of a football field. And unlike a deep-cycle submarine battery, the Hornsdale Power Reserve is designed not to provide baseload power for long periods but to kick in quickly to stabilise the power grid for a period measured in minutes, not days—a vastly different mission requirement. Utility storage systems have very different weight and volume requirements and safety regimes than a submarine.
There’s also an immense difference between the conditions for relatively close and short submarine patrols of a few weeks (generally European and Asian submarines) and the conditions for Australian long and distant patrols. ‘Long and distant’ entails a punishing regime of continuous deep cycling of the batteries dived at sea, while remaining safe and reliable for nearly three months. For ‘close and short’ patrols over a two-week period, with little or no transit to the patrol area, a submarine with air-independent propulsion (AIP) could spend the time at low speed without using its engines to recharge its batteries.
Woolner and Jones admit that the patrols of Australian submarines require a much bigger battery and generating power and, if chosen, a much larger AIP section than closer and shorter patrols. But it’s not simple to make everything bigger or replace lead–acid with a new chemistry.
As I wrote in 2016, replacing the lead–acid battery with a lithium-ion battery (or any light-metal battery) will require a completely new submarine design. Woolner and Jones argue that a new design should be started now for a battery that exists only in a laboratory. That’s impossible and would compound risk upon risk.
A main storage battery type and its size must be factored in at the start of the design phase because it will affect nearly every other system (over 70 for the Collins class). It will affect the weight, stability and trim (through location) of the boat; the size of the high-power cabling (and not forgetting bend radius); the electrical protection system; and the number of generators. It will also affect the electrical distribution network, the magnetic signature, the shock resistance, the main propulsion motor, the ancillary equipment, and even the air-independent propulsion system if one is included.
Nearly all proponents of lithium-ion or light-metal batteries concentrate on the high energy per kilogram characteristic. This is good for mobile phones, laptops, ground vehicles and aircraft. But this advantage of lithium or another light metal is also a vulnerability.
Due to the very high short-circuit currents and fast rise times, a lithium battery will need fire-hardened boundaries and advanced electrical protection systems. Each of the thousands of 500-amp-hour modules will need to contain safety-critical software-driven electronics to control voltages and currents within strict limits. At some stage during the life of the class, we could expect some failures. That would not make a good safety case for a submarine.
As a final shot, Woolner and Jones suggest that an advanced light metal–air battery would replace the original lead–acid battery, diesel fuel and engines together in one package by the mid-2040s, enabling a submarine to complete a full patrol on a single charge. I have run the numbers to check whether this is likely to be possible, for a generic 3,000-tonne conventional submarine performing an Australian submarine mission profile (see the online appendix to this post for details). My conclusion is that it is not.
A lithium-air battery (a new type of battery using oxidation and reduction of lithium to induce a current flow) would require some 4,000 tonnes of air (or maybe 800 tonnes of liquid oxygen) instead of the original batteries, fuel and diesels. That wouldn’t make sense unless it replaced an AIP plug. Significant development challenges yet to be overcome include chemical stability, capacity reduction and internal short-circuiting. The difficult development path and dependence on oxygen render lithium-air impracticable for a submarine design at present.
The Woolner–Jones predictions to the 2060s are theoretical performance projections from laboratory testing. The prediction is weight-based, and our submarines are volume-based, so to replace lead–acid the curve will be far less advantageous in practice.
From a submarine design perspective, I can only conclude that the suggestions are neither sensible nor practicable.
There’s no doubt that we need better submarine battery performance, which is the real focus of the Woolner–Jones proposal. What improvements do we want and how might we achieve them if that proposal is not the answer?
Reducing the battery charging (and therefore indiscretion) time for an Australian submarine is imperative. Their long transits require more engine time than for shorter range patrols. Submarines with little or no transit to the patrol area, and fitted with AIP, could run an entire two-week patrol at low speed without using a diesel engine to recharge their batteries.
We certainly need greater dived endurance, as Peter Briggs has written, including at higher speeds. This means we need longer time between charges, so beefing up battery capacity is the aim. Lead–acid batteries also lose capacity with each discharge–charge cycle, limiting the available energy to less than half the theoretical energy. It takes many hours to fully charge a lead–acid battery at reducing rates of power, to get that final 20% of battery capacity. Minimising that limitation would be very beneficial.
Lead–acid batteries require routine and lengthy ‘gassing charges’ followed by a top-up of each cell and then cleaning. A battery requiring little or no maintenance would mean more submarine availability.
Understanding what we want and what might be possible sets us on the right path to improved performance. It’s important to understand that the ‘state of the art’ in technology often differs markedly from the ‘state of the market’—what shipbuilders are actually delivering.
While underwater endurance may not necessarily be as good as that provided by AIP, Japan has begun replacing Stirling engine systems with lithium battery systems for its shorter patrols and has launched at least one such submarine. Japan has concentrated on battery chemistry, case hardening and software-critical battery management systems for safety management.
I remain unconvinced that this is the solution for Australia with its requirements for long transits and distant patrols and its stringent safety regimes.
Sweden continues to deliver new submarines with lead–acid batteries, although it is reviewing lithium chemistries. It’s also about to start testing a fifth-generation 150-kilowatt Stirling AIP module in the same footprint as the fourth-generation 75-kilowatt module.
I’ve seen no evidence that European builders have delivered a submarine with lithium batteries at sea. There are promises in advertising, but shipbuilders will want customers to pay for a risky development program.
Interestingly, the UK Ministry of Defence has awarded a contract to develop a new chemistry battery to replace the existing lead–acid emergency backup batteries in the Royal Navy’s Astute class. It’s chosen not to use lithium-ion but rather nickel-zinc due to its substantially safer chemistry and high energy density.
The continuing development of lithium (and light-metal) batteries is driven by commercial interests in mobile devices, ground transport and utility storage. There’s nothing wrong with that, but there is no big profit in submarine batteries, which are a small drop in the ocean of global demand compared with transport and utilities. And batteries for transport and utilities are not the same as for submarines.
So how do we upgrade a submarine to take advantage of commercially driven technology advances?
First, by improving capability in manageable stages—for example, using ‘drop-in’ replacement batteries, like the upgrade from 7,420-Ah to 8,400-Ah batteries we did in the Oberon submarines. The advantage of such a drop-in is that it could be tested on the Collins. Another way might be to lengthen the hull by adding a new section with extra capacity (like the Japanese or Swedish submarines). That, too, could be tested with a hull extension on the Collins. But for the Attack class, the extra length would make our submarine larger than its nuclear-propelled parent. We would be better to take the nuclear version!
Alternatively, there’s the full redesign. This is a big-bang approach with very high risks and costs and a long program schedule. It’s what Woolner and Jones appear to be suggesting, using a type of battery still being developed in a laboratory.
The changes they urge are radical with multiple parallel high-risk development activities. What is proposed is a no-win position for government—to choose an obsolete design now or to start a new design for the 2040s with theoretical projections from early laboratory testing.
However, Woolner is right to argue that there’s still a compelling need to improve submarine energy storage. The trick, though, is to plan properly for a transition to advanced batteries that are intrinsically safe, and that do not rely on complex safety-critical software-driven battery management systems.
Such batteries should be delivered as drop-in replacements and be tested at sea on the Collins.
Nickel-zinc may be a better option and should be the subject of an engineering development program such as the UK is undertaking.